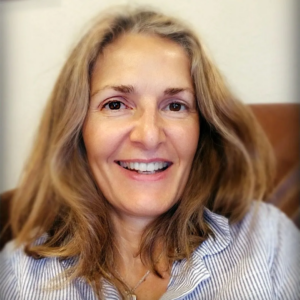
Pepi Maksimovic, director of application engineering at Ansys
To Pepi Maksimovic, director of application engineering at Ansys, the engineering simulation software company, the global manufacturing industry is a heat-wasting carbon emitter with wide targets for improvement. For Maksimovic, that viewpoint is just part of her job: She leads a technical team that helps customers improve their efficiency, reduce emissions, and, in some cases, design new technologies needed for a low-carbon future.
A handful of statistics paint the picture. Pumps, compressors, heat exchangers, mixers, furnaces, and other equipment are energy pits contributing to an industry that wastes about 65 percent as unused heat. Most of the emissions are in chemical manufacturing and refineries, and about half of the energy powering the manufacturing industry is derived from natural gas. The energy, the manufacturing machinery, and the processes within each plant can be transformed and optimized, Maksimovic said. Some already have been.
Simulation enriches and accelerates the ideation process. It spurs creativity. Once people start using it, the light bulbs turn on in their heads, and they want to use more of it — Pepi Maksimovic, director of application engineering at Ansys
On February 4th, Maksimovic will share insights from her work in a fireside chat on the main stage at Informa’s Sustainable Manufacturing Expo in Anaheim, California. In conversation with Chris Cantrell, ASME’s Senior Managing Director of Standards and Engineering Service, Maksimovic will discuss digital innovation and rigorous standards that support companies as they assess, validate, and scale sustainable manufacturing initiatives.
In advance of that conversation, Maksimovic discussed the role of engineering simulation software in building a sustainable manufacturing industry.
E4C: Let’s start with the problem. How urgent is it to improve the manufacturing industry?
PM: The timelines to hit the net-zero emission target by 2050 and meet the Paris Accord are tight. We have only two or three decades, pretty much, to act.
A lot of the technologies that are currently employed in the manufacturing environment have been around for decades or a century-plus. They’re mature, but we’re still finding areas to improve and refine and make them better. To achieve decarbonization goals, however, requires not only continuing to improve upon existing technologies but also the development, maturation, scale-up, and deployment of totally new solutions in a relatively short period of time.
We don’t have another 100 years to refine and improve. The pace of innovation must be accelerated. And that’s where engineering simulation comes in.
E4C:: Starting with the big picture, how can engineering simulation software help?
PM: It’s multi-fold. Let’s begin from the standpoint of environmental impact and efficiency. A factory or plant deploys equipment like pumps, compressors, heat exchangers, mixers, furnaces, heaters, etc. Every single piece of equipment consumes energy and adds to the carbon emissions created by the manufacturing process. It’s all cumulative. Simulation software can optimize the design and performance of the equipment for energy efficiency and emissions reduction.
Studies show that about 80 percent of the carbon footprint of a product—including manufacturing equipment—is locked in the materials it is made of and how it is manufactured. Simulation can help guide materials selection as well manufacturing techniques for improved sustainability.
Next let’s look at operational efficiency. Simulations can improve efficiency by reducing scrap rates, commissioning time, and down time and providing the ability to make operational decisions in real time.
For example, monitoring a manufacturing process to make changes as needed is typically done by installing sensors, followed by collecting and processing sensor data. By using simulation and creating so-called digital twins, an operator can put virtual sensors anywhere and extract data from wherever they want. The available data is collected from both physical data simulations. The information is greatly enriched and operators can act on the data almost instantaneously. To maximize efficiency, they can adjust the feed rate or change the RPM of a certain machine, for example, to control the yield and quality of the product, maximize the throughput and all the usual measures of manufacturing efficiency.
Digital twins are also used to improve energy efficiencies. In short, a variety of use cases can come into play.
Finally, simulation has a critical role in advancing innovations in zero- and low-carbon energy solutions such as nuclear, hydrogen, and others needed to decarbonize the manufacturing sector.
“Simulation enriches and accelerates the ideation process. It spurs creativity. Once people start using it, the light bulbs turn on in their heads, and they want to use more of it.” — Pepi Maksimovic, director of application engineering at Ansys. Photo: courtesy of Ansys
E4C: Can you share examples of companies that have benefitted using simulation software?
PM: Simulation software is used in all manufacturing industries: aerospace, automotive, materials, food, pharmaceuticals, semiconductor manufacturing, etc.
Plants that process materials are energy-intensive and operate around the clock. Process interruptions and unplanned downtime are costly, so optimization is critical, both from a financial and environmental standpoint. One glass manufacturer was able to reduce scrap by 30 percent by deploying virtual monitors in their production lines.
In another example, Verbund, a leading producer of in Austria, used digital twins for predictive maintenance and was able to save over $100,000 per year per turbine by avoiding unnecessary downtimes. Scaled across 100-plus plants in operation and the savings are significant.
Another energy company, TotalEnergy, was able to achieve 2 percent improvement in operations and save millions of dollars per year per refinery using digital twins.
Simulation is used to virtually model the myriad of processes that occur in manufacturing as feed materials are transformed into products. Those include heating and cooling, melting and solidification, combustion, ventilation, mixing, separation, forming, molding, casting, quenching, machining, joining, dipping and coating, crushing, conveying, packaging, additive manufacturing, visual inspection, and others.
E4C: What are some of the obstacles to adopting tools like simulation software to improve sustainability?
PM: None that are unsurmountable or complicated. One is not being familiar with simulation. Some smaller or more traditional manufacturing companies are just not used to using simulation technology or digital engineering.
E4C: Is it hard to learn to use the software? Is training an issue?
PM: That’s not really an obstacle nowadays. Simulation tools have become fairly straightforward to learn and use; user experience has come a long way compared to 20-30 years ago when it tended to be reserved for Ph.D.s and deep subject matter experts. Modern simulation tools have become more intuitive.
E4C: Are there other obstacles?
PM: Perhaps computational power. The relative cost of computing has gone down, but the complexity of the problems tackled with simulation increases as the capabilities of the software develop. Which is why high-performance computing, GPU computing, and cloud computing are commonly leveraged for speed and scale.
E4C: What are some of the ways simulations can influence the engineering design process?
PM: Simulation enriches and accelerates the ideation process. It spurs creativity. Once people start using it, the light bulbs turn on in their heads, and they want to use more of it. Simulation helps people drive all these engineering changes. They innovate. They get new ideas. That’s where you start seeing a lot of ideas rapidly fire up. And that breaks down the resistance to the tools.
See Pepi Maksimovic in conversation with Chris Cantrell at the Sustainable Manufacturing Expo in Anaheim, Calif., February 4th at 1:15-2PM Pacific Time.
A version of this article was first printed in Mechanical Engineering Magazine, available to members of the American Society of Mechanical Engineers (ASME). See the original version: Sustainable Manufacturing Needs Simulation.