As a laundry machine, this five-gallon bucket that spins on pieces of pipe might look the product of a trip to the junkyard. But its simplicity is deceptive. There are months of interviews, sketches and experimentation behind its humble appearance. And its designers have offered us a glimpse into their highly creative prototyping process.
Aaron Stathum and Eliot Coven, industrial design students at Philadelphia University, collaborated with Sudanese refugees at a job-placement service in New Jersey to design a low-cost human- powered washing machine. They wanted to make laundry day easier on people who wash clothes in a river. The end result is this plastic bucket with a neoprene cover.
To operate it, the user straps two loops of rope onto his feet and moves his legs up and down. Most of the materials are found objects. As such, the market version could cost less than $4 and it’s easy to make and easy to repair. At that price, it may be much cheaper than other human-powered laundry devices.
“We joke that our final product looks like a bunch of trash,” Stathum says. But using upcycled parts was the point, he says. Their design aimed to improved on existing products for the off-grid laundry market, and their research found devices with relatively expensive parts. Bicycle parts, for example, or injection-molded plastic pieces.
“The design community is so focused on these beautiful objects,” Coven says. “But who’s to say that [a clothes washer] has to be stainless steel and look like the Apple of laundry machines? Making it stylish would add cost and cost was our enemy throughout this project.”
Video demo
Nooradin Mohammad, a Sudanese refugee who helped with the design, shows how to assemble and operate the machine in this
brief video.
Developing World Washing System from Aaron Stathum on Vimeo.
Design notes
Stathum and Coven documented their experimentation process. Here, we can see pages from their sketchbook and the behind-the-scenes story of how the foot-powered washing machine took its current shape.
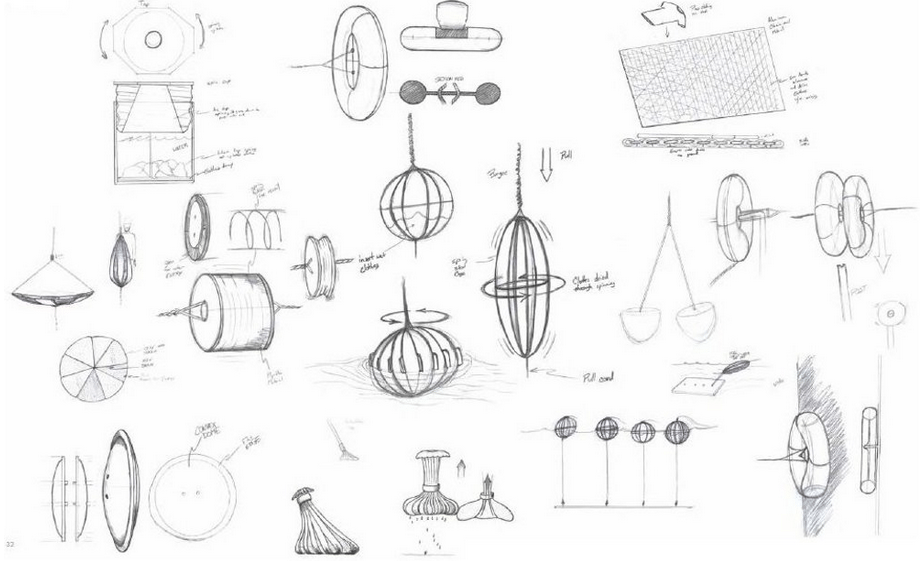
These sketches reveal some of the initial design ideas, many of which were discarded. The main element that survived the winnowing process of experimentation was the use of string. “That was the key moment for us when we figured out that we should use string instead of some other mechanical device. We think you can have access to string just about anywhere in the world,” Coven says. Image courtesy of Aaron Stathum and Eliot Coven
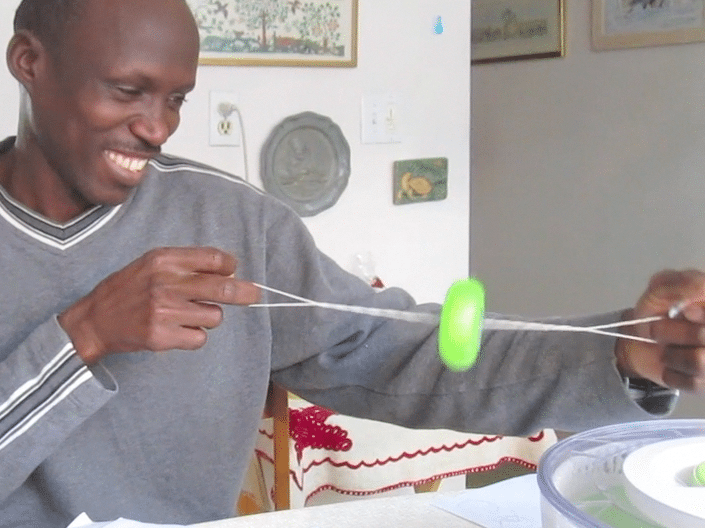
The designers based their early concepts on the spinning action of a string and a button. If you insert a string through a button and pull both ends tight, the button spins. Photo by Aaron Stathum
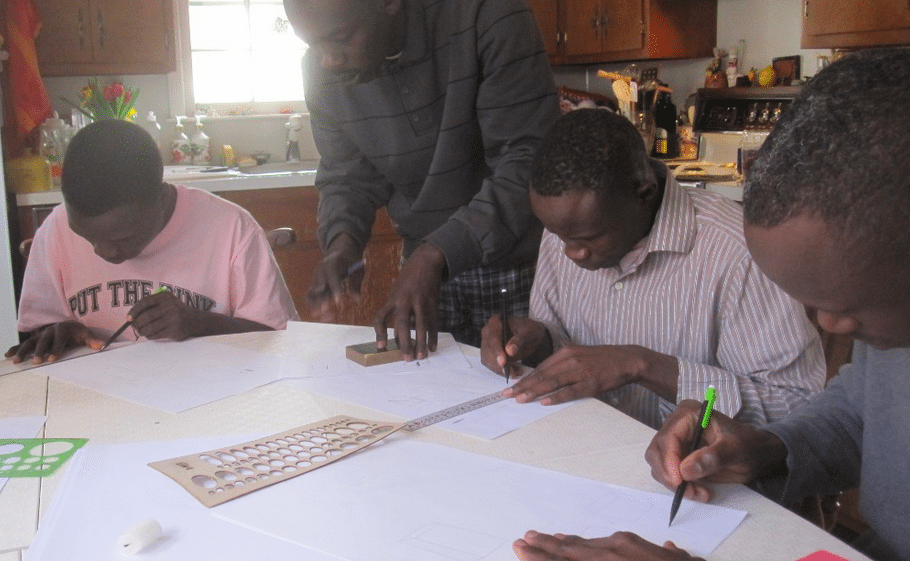
The designers collaborate with Sudanese refugees at a job placement organization in New Jersey. Photo by Aaron Stathum
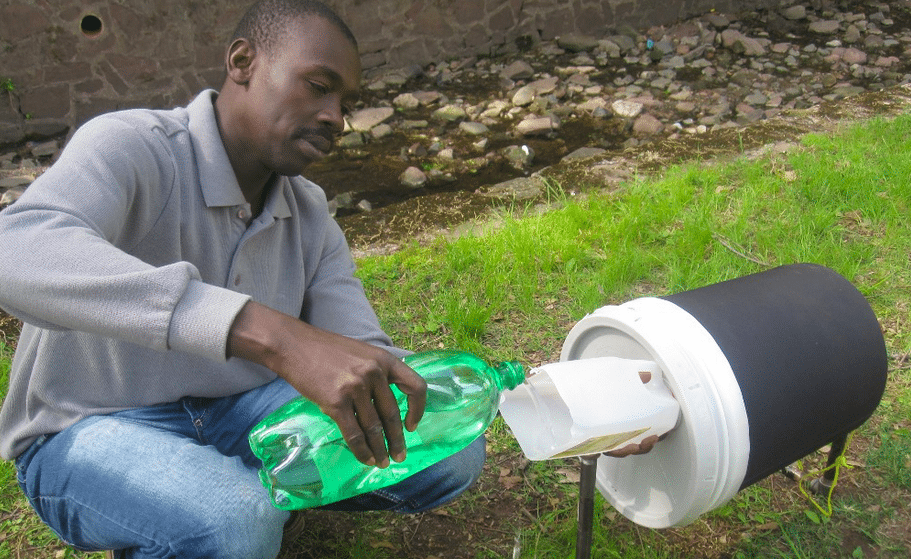
This is a demonstration of how to fill and operate the final version of the washer. Photo by Aaron Stathum
Next step
The design duo has their sights set on large-scale manufacture, and they say they would appreciate any assistance from the E4C community. Those interested can contact them through their Web site.