This report is available for full download to PDF.
Executive Summary
In response to the Kenyan government’s goal to build 500,000 homes under the Affordable and Dignified Housing Plan by the year 2022, Engineering for Change and UN-Habitat developed this research paper to present a cross section of appropriate construction technologies to guide and inform decision makers within Kenya’s Ministry of Transport, Infrastructure, Housing and Urban Development. The research was divided into two components. The first presents a case study of Brazil’s “Minha Casa Minha Vida” program conducted in 2009 to rapidly build 4 million homes. This study presents challenges of financing, implementation, and scale that were encountered during the effort. The second stage of research presents an analysis of appropriate construction technologies available in Kenya. Interviews were conducted with 12 construction professionals and manufacturers of relevant emerging construction technologies. The quantitative and qualitative data is then distilled into a graphic, comparable framework to assist Kenyan officials in understanding the benefits and limitations of the residential construction sector. A concluding discussion offers thoughts of the researchers and areas of additional consideration that extend beyond the scope of the research.
Introduction
In May of 2019, Kenya´s President Uhuru Kenyatta, in response to rising housing costs and increasing trends of rural-urban migration, declared that his administration would see to it that 500,000 homes would be built by the year 2022 as part of the Nation’s Affordable and Dignified Housing Plan (AHP). The AHP benchmarks provided by the Ministry of Transport, Infrastructure, Housing and Urban Development include that the unit cost of a home to be built should not exceed 305 USD (~ 30,500 KSH) per square meter. The provided details also call for different housing types to be provided according to three income ranges: 125,000 units for social housing programs; 225,000 of low-cost units; 150,000 units to resolve ‘mortgage gap’ of middle income earners. In response to this commitment, UN-Habitat, an office of the United Nations which seeks to promote sustainable urbanization as a driver of development and strives for adequate shelter for all in Kenya and abroad, has partnered with Engineering for Change (E4C) to develop this rapid performance-based review of emerging construction technologies that are available locally and internationally. The intention of this study is to help inform strategic planning towards achieving the government’s goal by 2022.
Of the appropriate technologies reviewed for the administration’s consideration, some are well known and commonly used in the region, while others are in the early stages of prototyping and are being developed outside of Kenya.
Our findings indicate that the technologies with lower environmental impact are Compressed Earth Block (CEBs), Interlocking Soil Stabilized Bricks (ISSBs) and Compressed Agrofiber Panels (CAF). CEBs and ISSBs however are not so urban appropriate, as they each depend on the availability of large amounts of inorganic earth for fabrication. When considering the urgency and timeframe of the project, the speed of construction and assembly of each technology were also reviewed. The systems appropriate for fast-track project delivery were found to be full scale 3D Printing, Expanded Polystyrene Panels (EPS), CAF, and prefabricated Steel Frame (SF) structures. The most cost-efficient technologies are CEBs, ISSBs, EPS CAF, with EPS and CAF as more appropriate options for urban areas. Additional factors such as durability and fire resistance were considered and compared.
The list of housing construction technologies presented below does not intend to indicate which system is “the best”, nor does the research indicate which technologies should be adopted and employed. The research does however provide information on cost, efficiency, and possibility. This information can be used by UN habitat and the Kenya government to strategize and plan its implementation in order to achieve the stated goals of the AHP by 2022. The concluding discussion seeks to broaden the conversation of both “appropriate technology” and of “affordable and dignified housing” to consider issues of new development, upgrading, and urban planning.
Methods
Tasked with developing a visual presentation on appropriate construction systems for Kenya’s Ministry of Transport, Infrastructure, Housing and Urban Development on behalf of the UN-Habitat office in Nairobi within only four weeks, the E4C team developed a research methodology that sought to develop a cross section of comparable technologies to guide and inform Kenyan policy makers. The research was divided into two components: a case study of Brazil’s “Minha Casa Minha Vida” (PMCMV) program implemented in 2009 to rapidly build 4 million homes, and an analysis of appropriate technologies available for use by the ADH program in Kenya.
The Brazilian case study was conducted through a research of academic publications and performance-based reports about the housing construction efforts and the socio-economic aspects of the PMCMV Program. Economic data (Abranic, 2019) and qualitative studies on the housing units produced in the context of PMCMV (Rede Cidade e Moradia, 2012) were analyzed and summarized in order to present relevant takeaways applicable to the proposed Kenyan program.
The second component was an analysis of 6 different construction systems that might be used for affordable housing construction in Kenya. The list of technologies reviewed was determined by the E4C Fellows, the UN-Habitat team, and informed by the interests of the Kenyan Ministry of Transport, Infrastructure, Housing and Urban Development. Background research on each system was conducted through a review of promotional material from manufacturers and on-the-ground reporting from experienced builders and engineers. Information gathered in this phase was then used to develop interview questions that would enable the research team to quickly summarize and compare the available technologies.
Interviews with manufacturers of relevant construction products and systems were then conducted on Skype over the course of 15 days in semi-structured formats. Subjects were briefed on the goals of the study, then asked to summarize their company’s objectives, accomplishments, and goals. Towards the conclusion of the discussion two hypothetical questions were put forward to the interviewee:
- A request to explain their company’s capacity to deliver 2,000 homes under a tight time frame in rural or urban Kenya.
- A request to estimate the time and cost to build a 40 square meter home using their company’s system of construction.
Responses were recorded and logistical/supportive challenges that were expressed by the interviewee were documented. Summaries of each interview are annexed at the end of this document.
Data from the review of promotional material and from individual interviews was then aligned across a comparative framework that quantifies various considerations including time of construction, material wastage, cost, and environmental impact. Each criteria of measurement was then comparatively rated across five levels, from “Very low” or “Poor”, to “Very High” or “Excellent”. These results were then visualized and color coded into a “snapshot” to assist Kenyan policy makers in understanding the benefits and limitations of each system. A small number of comments were then provided at the conclusion of the presentation to suggest additional areas of consideration.
Brazil Case Study: Learning Forward
Brazil’s Minha Casa Minha Vida program was a government subsidized housing development program implemented in 2009 that sought to reduce the nation’s housing deficit. Ten years later, this program is considered to have been successful because more than 4 million houses were built. It has also been widely critiqued, however, for reasons including a lack of consideration of land values and minimal public space design. Considering the scale and timeline of this initiative, the successes and failures of this initiative can provide relevant insight into challenges that could confront Kenya’s AHP.
Construction partnerships under the Minha Casa Minha Vida program were primarily forged through the private sector, while financing packages were established through public lending institutions according to a family’s income levels. Approximately 90,000 units, representing 3% of the total 4 million homes constructed, were built by cooperatives and organizations from the non-profit sector; though these were also financed by Caixa Econômica Federal (the nation’s public bank). In both cases houses were only made available for purchase, not for lease or rent.
The MCMV Program’s most used technologies were Structural Masonry and Reinforced Concrete. In both systems the walls are responsible for transmitting the vertical and horizontal loads to the foundations, which were designed to stand up to hazardous weather and earthquakes. In addition to reasons of structural resilience, the technology also allowed for the production of replicable designs to be fast-tracked to completion. A measured decision was made to prioritize these systems for their strength and low cost in spite of the large carbon footprint associated with cement-based construction.
The lending structure for home purchases was divided across four income levels, with annual interest fees tailored accordingly.
Table 1. Lending structure for home purchases in Brazil’s Minha Casa Minha Vida program.
Notable achievements of the MCMV Program were largely economic. According to Abranic (2019) the program is directly credited with an increase of 13% in formal jobs in civil construction sector from 2009 – 2017. These gains resulted in an increased tax revenue in the sector that proved to be higher than the subsidy provided (~5.6 billion USD/year), resulting in an estimated 0.33% increase in GDP. Upon completion of the program in 2017, 70% of construction sector GDP related to the programs investments, indicating a strengthening of national capacity in housing development. Additionally, 45% of house production was allocated to family within Income Range 1 (Social Housing) reflecting a program that followed through on its intention to provide homes for Brazil’s most vulnerable families.
While the MCMV Program proved to be a financial benefit to the nation, qualitative and geographic challenges were identified that bring the processes of implementation and equity of distribution of the program into question. In order to achieve the large volume of houses targeted, large residential complexes were developed on the periphery of urban areas where land values were lower and less accessible, and less desirable. This apparent lack of planning and consideration of zoning and land use left these planned developments with poor access to transportation infrastructure, reducing residents’ urban mobility and access to zones of employment. Furthermore, this prioritization of mass housing over neighborhood building can be seen in a severe lack of public space. An additional lack of consideration of the social dynamics present between communities also led to conflict, making the newly planned housing developments even less desirable for potential residents. Finally, in only very few cases of development projects executed by non-profits, were steps taken to build with renewable materials with an intent to minimize the project’s environmental impact.
All of these factors resulted in the development of the MCMV program to be economically productive and quantitatively successful. The qualitative social and cultural complexities however bring the long-term success of the program into question, as further challenges may yet emerge.
Technology Trends
Data on technologies presented below are based upon findings from multiple interviews. While some expectations were confirmed, some results were revealing of unexpected benefits and challenges. All technologies show potential and could be employed in Kenya to help achieve the AHP goals by 2022.
3D Printing
Interviewed companies: Icon 3D (USA) / Winsun (China)
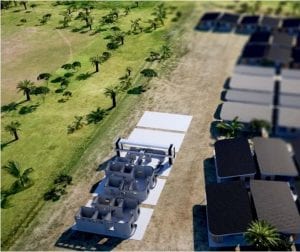
3D printing (photo by ICON 3D)
Full scale 3D house printing technology is a construction method that uses a large 3-D printer-scaffolds to build the walls of a structure. It can be used to build on-site or to produce pre-fabricated components remotely. The 3-D printer “ink” is typically a cement-based mixture that can include additives to improve strength or reduce cost. Mixtures can include building demolition rubble, proprietary additives to the cement base, fiberglass, or special glue mixes. The cost of production can vary from 225 – 250 USD/m² of a single story wall structure for a home. The price referenced considered the construction of only walls (roof, foundation, claddings, finishings, wiring and plumbing are not considered). Depending on the availability of material, a typical printing scaffold and team can print the walls of a 40 m² house within approximately 24 hours (workers still have to finish the roof and claddings). The technology can be implemented in rural and urban areas, though is most easily applied in flatlands. While 3-D printing systems may require only a small workforce at the time of printing, a highly qualified operator is needed and skilled craftsmen are needed for follow up installation of architectural elements.
Companies interviewed communicated their capacity provide multiple designs for 3D construction embedded within the hardware of the printing system, allowing builders to select and vary designs from site to site. Both companies interviewed however mentioned that this technology is not appropriate for the pouring of structural footings and foundations. A cured (and presumably reinforced) concrete slab would therefore have to be poured in advance of any printing, and the design of the slab must align with the design of the home that is selected for printing. As this 3D printing technology is still in its infancy, the systems reviewed cannot be used to complete elevated slabs or roofs. Complementary systems therefore would have to be designed in concert with the 3D printed forms. Additionally, reports of multi-storied 3D printed structures could not be verified. Companies interviewed indicated that only single story homes have been completed with this technology.
Compressed Stabilized Earth Blocks (CSEB)
Interviewed companies: DwellEarth / Pandabrick
Compressed Stabilized Earth Blocks (CSEBs) are made by mechanically compressing inorganic soil mixed with a small portion of Portland cement (5-10%) into a brick. Walls of CSEB are built using standard bricklaying and masonry techniques including the use of clay or cement mortar. CSEBs require substantially less energy to fabricate than conventionally fired bricks.
The cost of production of standard CSEBs can vary from 190 – 250 USD/m² when considering quantities for a conventional one story home. Prices referenced include a complete house and workforce (CSEB walls, concrete foundation and floor, gauge roof, doors and windows) though do not include wiring and plumbing. Construction takes approximately 7 weeks to complete 40 m² house, from brick production to substantial completion. This includes 7-10 days for curing of the bricks, which is a process best accommodated on site. This technology is more suited for rural areas where large amounts of inorganic soil are present. A small team of masons can be quickly trained to mix material and fabricate the bricks, though a qualified foreman is needed to ensure quality control. An additional consideration is that waterproofing sealant must be applied to the external faces of the brick after completion of the home. This must then be reapplied every 3-5 years to ensure that the wall systems do not succumb to erosive forces.
Interlocking Soil Stabilized Blocks (ISSB)
Interviewed companies: DwellEarth / Pandabrick
Interlocking Stabilized Soil Blocks (ISSBs) are a specific type of Compressed Stabilized Earth Block (CSEB) technology. While ISSBs are made from the same soil/cement ratio of 1:10 as CSEBs, ISSBs present an interlocking form that allows for strong, rapidly assembled systems that do not need cement mortar. Compression machines for brick fabrication can be powered by diesel fuel or electricity, or be operated with hand power. ISSB fabrication is less expensive and requires less energy than conventional brick firing methods.
The cost ISSBs are comparable to CSEBs, varying from 190 – 250 USD/m² for a 1 story home. Construction takes approximately 7 weeks to complete a 40 m² home, from brick production to substantial completion. This includes 7-10 days for curing of the bricks. This technology is more suited for rural areas where large amounts of inorganic soil are present. A small team of masons can be quickly trained to mix material and fabricate the bricks, though a qualified foreman is needed to ensure quality control. An additional consideration is that waterproofing sealant must be applied to the external faces of the brick after completion of the home. This must then be reapplied every 3-5 years to ensure that the wall systems do not succumb to erosive forces.
Expanded Polystyrene Panels (EPS)
The E4C research team attempted to contact distributors and advocates of EPS technology in Kenya for discussions but were unable to secure such interviews within the timeframe of the study. One of the E4C researchers however has direct design and construction experience with the product in Kenya. This experience and as well as promotional material has been consolidated into the review below.
Expanded Polystyrene (EPS) technology is a construction system of prefabricated panels that are extremely light and can be easily transported from fabrication to construction sites. Assembled from ready-made EPS foam sandwiched between galvanized steel wire mesh, the panels are then tied together on site and plastered over with a cement-based mixture. The panels can be easily modified on site with wire cutting tools, making the system versatile and can be easily incorporated with complimentary construction systems.
Expanded Polystyrene (EPS) technology is a construction system of prefabricated panels that are extremely light and can be easily transported from fabrication to construction sites. Assembled from ready-made EPS foam sandwiched between galvanized steel wire mesh, the panels are then tied together on site and plastered over with a cement-based mixture. The panels can be easily modified on site with wire cutting tools, making the system versatile and can be easily incorporated with complimentary construction systems.
Manufacturers of the system often have additional specialty components available for purchase. These included wall panels of varied thicknesses, floor panels, and stair systems. Under the direction of a licensed engineer, EPS panels can be used to build up to 20 stories.
Compressed Agricultural Fiber (CAF)
Interviewed companies: Ekopanely / Pumapa Capital
Compressed Agricultural Fiber (CAF) panels are insulated panels made of agriculture waste such as wheat and rice straw. The agri-waste is compressed at a high temperature and sealed with a final layer of cardboard. Prefabricated offsite, the panels are light weight and easily transported to a construction site. While the panels can be self-supporting, the system is best paired with a steel or wood frame structure as a primary structural system.
Cost of construction can vary from 190 – 240 USD/m². Price considerations include a complete house and workforce (CAF panels, concrete foundation and floor, roof, doors and windows), and exclude wiring and plumbing costs. The time of construction for a complete house is about 4 weeks. Depending on the fiber available, the construction method can achieve an almost zero carbon footprint.
Steel-frame
Interviewed companies: FasBuild / Steel Home Company
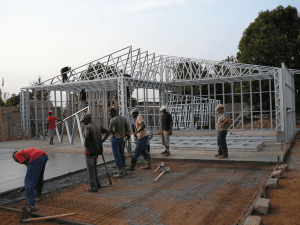
Steel Frame: Steel Home Company
Steel frame construction is defined in this analysis as a rapid assembly system that is pre-cast, packaged, and delivered for assembly on site. The primary structural components, extruded steel channels, are made from thin gauge high strength galvanized steel sheets. Sections are joined together using rivets or self-tapping screws to form structural bays and/or roof structures. While entire homes can be packaged for international delivery (typically 4-5 homes per shipping container), portions of homes and individual components (i.e. roofs) can also be designed and packaged for onsite assembly and installation. Additionally, the framing system can be designed to accommodate different infill panels to standard masonry systems.
Construction cost can vary from 250 – 350 USD/m² for a steel frame home. The estimated price considers a complete house and workforce (walls, concrete foundation and floor, roof, doors and windows), though does not include wiring and plumbing. While this is the most versatile and most complete home construction system reviewed in this study, companies interviewed indicated that a cured slab of concrete would need to be poured in advance of any onsite assembly. Once this slab is in place, construction of a complete 42 sqm home can take approximately 7 days.
Companies interviewed for this system of construction are based in South Africa and are looking to expand to other regions of Sub-Saharan Africa. While most talking points surrounded the opportunities and challenges of fabrication for international transport and delivery to Kenya, the possibility of establishing a fabrication plant in Kenya was also offered as a possibility that could be considered.
Comparison
The comparison table presented below intends to assist decision makers in broadly understanding the state of presented technologies. Data from the review of promotional material and from individual interviews was aligned across this comparative framework to quantify various considerations including time of construction, material wastage, cost, and environmental impact. Each criteria of measurement was then comparatively rated across 5 levels, from “Very low” or “Poor”, to “Very High” or “Excellent”. These results were then color coded (as initial research was communicated over a single slide) into a “snapshot” to assist Kenyan policy makers in understanding the benefits and limitations of each system.
Visual analysis of the framework sufficiently reveals that no single technology stands out above the others as particularly low cost, easily and quickly assembled, while also boasting a small carbon footprint. Also, while no single technology can be used independently to construct an entire building (all options require a concrete footing), different systems can be paired together to achieve desired timelines and reduced carbon footprints within an established budget. Additionally, while some systems are most appropriate for rural construction locations, others present qualities that make them well suited for urban environments.
Table 2. Construction methods comparison table.
Conclusion
Each of the technologies presented within this paper could be used towards achieving the goals of the AHP by 2022. Combinations of the technologies studied or designs that incorporate such technologies with or more conventional construction systems could be considered. Architectural design firms and experienced contractors should be consulted to consider the most appropriate combinations of systems for any proposed building locations.
Aside from construction systems, considerations and priorities should be shaped in response to both the lessons learned through Brazil’s MCMV program, as well as the uniquely Kenyan urban and rural environments. Rural and peri-urban initiatives should be considerate of connectivity to both infrastructures of water and energy, as well as to transportation corridors to facilitate connection to jobs and industry. Not only would such advanced infrastructure planning reduce the likelihood of encountering problems similar to those exhibited in Brazil, but it would also align housing development initiatives to support an additional agenda item of the President’s Big 4: manufacturing. Further, towards achieving affordable and dignified housing for all, allocation of new construction in urban areas should be based upon selective criteria. Achieving affordable housing can a times be achieved only through financial interventions, incentives and programs. Dignified housing can at times be achieved through only improved service infrastructure; the resolution of land ownership; or the considerate design of public space.
Edited by: Grace Burleson
Additional contribution: Eddine Sarroukh, Mariela Machado
Hey my name is Samson Micubu and I love the report you have done. I’m interested with the Compressed AgriFiber panels (CAF) since currently I’m doing a research on it’s adaptability here In Kenya. I would greatly appreciate if you shared what you know about that technology or even the local manufacturers and players of it .
My email is mtechysam@gmail.com