Executive Summary
China’s manufacturing industry is characterized by production of majorly low-cost commodities in the consumer goods sector. Labor-intensive methods of production with a rudimentary level of automation and limited digitization are used, lagging far behind Industry 4.0. However, international competition is pushing many Chinese manufacturing firms to consider more efficient methods of production and invest in domestic Research and Development (R&D). These financial motivations coupled with Chinese firms’ overall lack of integrated sustainability strategies led the government to enact the Made in China 2025 initiative oriented to boost the Chinese manufacturing industry into the “factory of the world”. This initiative combined with the global driver of sustainability presents several pathways for Autodesk including (1) continued focus on the development of software and systems that enable smart manufacturing, including big-data and sensors, (2) development of tools specifically for increased growth in domestic R&D, and (3) securing support from government agencies and focusing on products for the following industries: aviation, automotive, electronics, metals and materials, energy equipment, food and medicine and ship building.
1 Introduction
With ongoing global advancements in technology and green innovation, organizations and governments have established strategies and policies to conserve the environment while increasing manufacturing capacity and production. China is a particularly interesting case considering the country’s immense economic growth and recent establishment of stricter environmental protection laws.
The goal of this study is to analyze the Sustainability Approach for Autodesk in China based on the prevailing conditions in both the market and the manufacturing industry. Chinese manufacturing and sustainability initiatives are analyzed and compared to other developed economies. An analysis of trends in the manufacturing industry, digitization of processes, the Made in China 2025 Initiative, and the economic and environmental challenges in the industry is presented. Further, the drivers of sustainability, implementation, and efficiencies in manufacturing are discussed.
2 China Market Analysis
Over the last three decades, China has become an economic world leader, second to only the United States. China continues to expand at nearly three times the pace of the United States, with an annual growth rate above 9%.1
China’s economy is dominated by electrical and computer machinery exports.2 While the service sector contributed to more than 70 percent of the economy in many developed countries, China continues to focus on its manufacturing industry; including home appliances, clothing, auto, consumer goods and agricultural means of production.
2.1 Local Market
Domestic manufacturing of consumer goods makes up the majority of the local Chinese market. Here, manufacturing is characterized by low-tech, labor-intensive production methods. Rather than investing in advanced and high-tech manufacturing processes, local firms rely on the presence of a large local labor force willing to work for minimum wages.
As part of the country’s environmental protection initiatives in the local market, the Chinese government has invested heavily in material recycling. This industry relies on manual labor with thousands of people making a living by sorting waste, selling recyclable items to specific firms, and disposing of remaining waste in landfills.
Within the automotive, aviation, and medical equipment industries, the local market functions at various efficiencies:
Automotive Industry
According to the China Association of Automobile Manufacturers (C.A.A.M), automakers in China delivered 28,226,616 passenger and light commercial vehicles in 2017. Germany’s Volkswagen remained the best-selling brand followed by Japan’s Honda. The third best-selling automobile was a Chinese brand, Geely. Korean and American sales suffered with Hyundai (Korea) dropping from the top ten and General Motors and Ford (United States) both falling below local Chinese brands.
Medical Equipment
China’s low-tech medical device market consists of small and medium-sized enterprises (SMEs) and is dominated by domestic companies. The market is highly saturated with nearly 3,000 SME Chinese medical device manufacturers, each with limited market share. Furthermore, these companies tend to possess only a handful of profitable products, most of which are from high sales volume of low-tech products. However, the domestic medical devices industry is advancing with some firms entering into the mid-level market. In doing so, these firms are taking advantage of an average 30% lower production cost compared to that of foreign competitors.
China’s medical device market is expected to continue growing rapidly, mainly driven by the government’s aim to advance community healthcare centers in rural China. As part of the greater healthcare reform initiative, the government allocated USD 250 million to subsidize medical equipment purchases in China’s rural regions. This investment will likely focus on the low-tech products and equipment that are in high demand in rural hospitals and clinics.
Aviation Industry
In the last five years, revenue for the aircraft manufacturing industry in China grew at an annual rate of 11.7%. In 2018, total revenue is set to rise 6.9% to an estimated $63.4 billion. This growth is attributed to the rising demand of domestic aircrafts and repair services, and government-sponsored defense programs. In 2011, branch airlines were exempt from airport construction fees, which further stimulated domestic demand. The government has also increased support for Chinese aircraft manufacturers, incentivizing aviation research, development, and manufacturing of large aircrafts. Exports are expected to increase 0.6% from 2016 to total $3.4 billion in 2018, accounting for 5.4% of total industry revenue.3
2.2 International Market
To cope with the international growth trends and pressures from the United States and Europe, China has set several measures particularly focusing on the automotive, medical, and aviation industries. In particular, the Made in China 2025 initiative, established in 2015, which aims to upgrade the country’s manufacturing of high-tech products, further discussed in section 3.4.
Automotive Industry
Included in this initiative is a focus on the development of clean and fuel-efficient vehicles in an effort to sustain continued growth of China’s automobile industry. Priority has been given to facilitating the research and development of electric, hybrid, and alternative fuel-burning vehicles.
Since 2008, China has boasted the highest annual production rate of automobiles in the world, exceeding that of the United States and Japan combined. In 2009, the number of registered cars, buses, vans, and trucks on the road in China reached 62 million and is expected to exceed 200 million by 2020. This growth is spurring demand for automotive parts, services, and after-care products. China’s largest domestic car manufacturers are SAIC Motor, Dongfeng, FAW and Chang’an. Although the majority of Chinese vehicles are sold domestically, 956,000 units were exported in 2017.4 China’s high demand for domestic automobiles has improved the country’s automobile manufacturing infrastructure, which policymakers hope will enable Chinese automakers to soon become more competitive on a global scale.5
Throughout China, cities are beginning to hold commercial and consumer vehicles to higher emissions standards. In major cities, such as Shanghai, passenger vehicles are required to meet Euro-3 emission standards. In 2008, Beijing became the first city to require light-duty vehicles to meet China-4 emission standard, which was equivalent to Euro-4. Beijing shifted its emission standards to the fifth-stage standards for light-duty and heavy-duty vehicles in January 2013 and August 2015, respectively. In April 2016, the Ministry of Environmental Protection (MEP) released the proposal for light-duty China-6 standard.
Aviation Industry
The Chinese aviation industry continues to grow due to the rising domestic demand for aviation services coupled with the government’s heavy investment in aviation research and development. This growth has raised China’s demand for aviation material imports for domestic, foreign and joint entities.
At the end of 2017, China’s civil fleet totaled 3,296 aircraft.6 The Boeing Company predicts that demand in China will increase to 7,240 new aircraft over the next 20 years, which is a value of nearly 1.1 trillion USD.
In 2018, the Boeing Company delivered a record high of 202 new aircraft to China, representing 26 percent of the company’s global deliveries and its sixth consecutive year of more than 140 deliveries to China. Another U.S company, Bell Helicopter, also experiences high demand from the Chinese market. In 2017, Bell Helicopter signed a deal for 100 Bell 407GXP single-engine helicopters with its Chinese partner, Shaanxi Helicopter.
According to the Bell Helicopter Vice-President of Marketing and Sales, the Chinese market is increasingly bringing business opportunities to suppliers and partners throughout the aircraft supply chain, in addition to being one of the United States’ “big buyers” of aircraft. China’s domestically-developed C919 large passenger plane, ARJ21 new regional jetliner, and Y-12 general aircraft all include U.S-made components. Overall, China’s aviation market has high growth potential with many opportunities for international companies along their supply chain.
Medical Equipment
More than 70% of Chinese medical devices fall into one of four categories: (1) Diagnostic imaging devices, (2) Medical supplies (3) Orthopedics and implanted medical devices, and (4) Dental. Nearly 15% of Chinese medical devices currently in use were manufactured in the 1970s, meaning that this industry is in need of some upgrades. The government has announced its intention to replace older devices to improve the quality of care available.
Following the United States and Japan, China’s medical device market is currently the third largest worldwide7 with an annual revenue of $53.62 billion USD in 2015.8 With annual growth rates above 10%, China is expected to surpass Japan to become the second largest medical device market within five to seven years.
Currently, China relies on imports from the United States, Japan, and Germany to meet their domestic medical device demand. Nearly 90% of high-tech devices, which account for 70% of China’s medical device market, are foreign-made. Among the industry’s top ten manufacturers in this sector, seven are foreign invested firms or joint ventures. These companies have targeted China’s high-end medical device sector and have established a dominant presence in many of the leading high-end product lines, currently constituting more a large share of China’s high-end medical device market. Many Tier-IIIi hospitals specifically require imports to meet the demands of wealthier patients; particularly for cancer, cerebrovascular disease, and cardiovascular disease.
Impact of Trump Tariffs on China’s Market
According to Forbes Magazine, U.S-based companies are shipping back and forth from China to avoid tariff lock-in dates. As of September 2018, the recently enacted tariffs by US-president, Donald Trump, have not harmed China’s international trade. Total trade activity climbed 12.9% on an annual basis in August in yuan terms, up from 12.5% in July. In dollar terms, total trade grew 14.3% including an export expansion of 9.8% which exceeded market expectations of 7.8%.9
Despite these tariffs, in 2017, exports of steel and aluminum increased by 10% and 32%, respectively. Personal computer components, a large target of the tariffs, still increased by 6.7%.10 Exported semiconductors continue to be a driver of economic growth but appear to be declining. While the last quarter saw a growth of 15.8%, this is much lower than the 29.0% seen in the prior three quarters. Consumer exports are fairly stable with apparel exports up 1.0%, footwear down 1.5%, and toys up 3.8%. Overall, trade between China and the United States saw an equivalent annual rise of 11.3% and 18.4% in July and August 2018, respectively, leading to nearly $301 billion total trade on the year.11
Although China remains largely unscathed by the recent tariffs, it is expected that the U.S market will begin to lessen their dependency on Chinese-produced products. Thus, China aims to strengthen their export base to other counties to supplement for the items and components with stringent U.S tariffs.
2.3 Comparison of China, US & Europe Markets
During the last decade, trade and investment relations with China have been of increasing importance to U.S and European machinery manufacturers due to its presence as a major export market, a reliable components production base, and a growing economic competitor.12 The Chinese market focuses on low-cost and high quantity manufacturing while much of the manufacturing in the U.S and Europe is high-tech with large profit margins. Unless Chinese manufacturers acquire a comparable level of technology, U.S and European manufacturers continue to have a competitive advantage in the high-tech sector.
The manufacturing sector in China remains very profitable with a sales value estimated at USD 300 billion, which includes 88.5 billion accounted for by Foreign Invested Enterprises (FIEs). However, Chinese companies aim to advance their technical quality by investing in research and development (R&D), technology transfers, and copying of foreign innovations. The market position of U.S and European companies is predicted to be threatened and their profits expected to fall.
China’s ongoing growth in manufacturing capacity, in an already saturated domestic market, continues to increase the number of exported products, which are competitive internationally due to their low costs. However, it is expected that Chinese companies will attempt to enter more advanced markets due to increased competition from other low-cost manufacturing markets such as those from Southeast Asia. This shift is likely to result in increased pressure on Chinese companies to increase R&D or further exploit foreign-owned Intellectual Property Rights (IPRs). Concurrently, U.S and European investors are increasingly facing barriers to market access due to investment restrictions, loss of IPRs, and competition from subsidized competitors. Additionally, import laws are not always followed by Chinese authorities and there is a growing concern of corruption in Chinese trade, such as implementing barter deals for oil.
Additionally, China’s Belt and Road Initiative (BRI) aims to improve transportation and connection between Asia, Europe, and Africa. This $900 billion initiative intends to increase trade and expedite development in the region.13
International competition has pushed many Chinese companies to consider more efficient methods of production to improve their financial sustainability and increase their positionality in the global market. This is reflected in an increase in “smart factory” implementation with 25% of factories currently operating under this initiative and 53% working towards smart factory adoption.
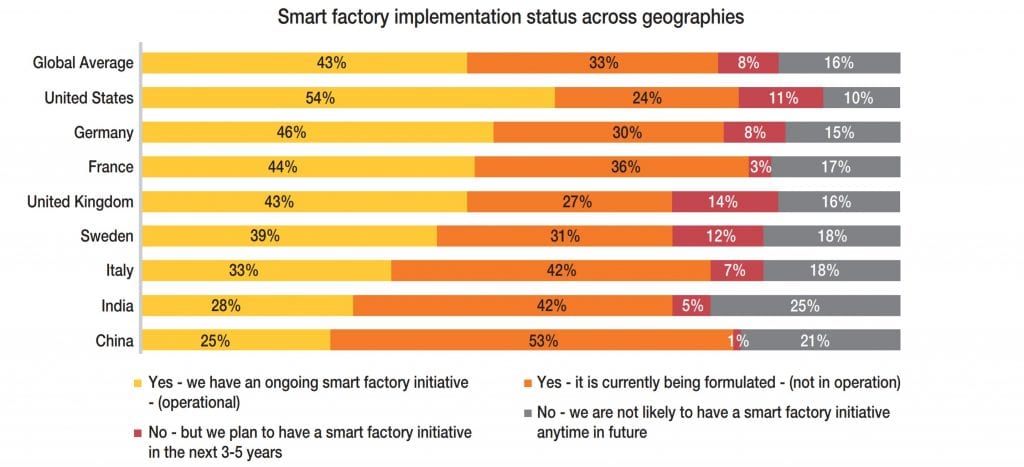
Source: Capgemini Digital Transformation Institute, smart factory survey, Feb-Mar 2017.
Implementation of smart factories can increase the quality of product. The ABB plant in Beijing saw a decrease in lead time from eight to two days while also increasing the percentage of reliable deliveries to 99.94%. Although adoption of smart factories is spreading across Asia, particularly in the industrial manufacturing (67%) and aerospace (62%) sectors, China still lags behind North America and Europe by 20-30%.14
3 Industrial Analysis
In China, many factories utilize a rudimentary level of automation and almost no digitization,15 lagging behind other industrialized countries. Technology leaders such as Germany and Japan, in contrast, make use of highly automated production lines and information technology management processes. Chinese enterprises use an average of 49 industrial robots per 10,000 employees, compared to 531 in South Korea, 301 in Germany, and 170 in the United States.16 Furthermore, this calculation from China excludes migrant workers, which lowers robot density even further. Low use of automation can be attributed to upfront machinery and initial operational costs.17
Source: China Manufacturing 2025, Putting Industrial Policy Ahead of Market Forces (2017).Worldwide, highly industrialized regions and economies are beginning to adopt so-called Industry 4.0, a combination of automation, data exchange, and internet of things (IoT) used in manufacturing. Germany was a key pioneer of Industry 4.0 with their government’s High-Tech Strategy 2020 Action Plan. The European Union (EU) has developed the Horizon 2020 plan entitled “Factories of the Future.” France and the United Kingdom have also pushed their initiatives, “Industry of the Future” and “High Value Manufacturing Catapult Programme,” respectively.18 This international movement prompted China to develop the Made in China 2025 Initiative for sustainable development.
3.1 China’s Manufacturing Sector
China remains one of the largest manufacturing countries in the world. According data from the World Bank report of 2011, value added in China due to manufacturing was $2,330.68 billion USD, representing 20.3% of the global manufacturing value added. This industry has contributed greatly to China’s economic growth, particularly since the country’s marketization reform and participation in the World Trade Organization (WTO).19
Even with this massive growth, the Chinese industry faces several challenges including the rising costs of production and shrinking export market of low-cost products. Currently, China’s manufacturing industry focuses on processing and assembly, which present the lowest value in the chain. In terms of patent technologies and purchase of the upstream resources, China still depends on other economies such as Europe, U.S, and Japan, which control most of the resources. At present, the Chinese government is working to change their position internationally.
3.2 Industrial Processes
Globally, production methods have transitioned to incorporate technological advancements and become more efficient. So-called Industry 1.0, the first stage of the industrial revolution, relied on steam and water power for manufacturing. Next, Industry 2.0 incorporated electricity to power machines and mass production. Industry 3.0 introduced industrial robots, programmable logic controllers, and IT-based production management. Most recently, Industry 4.0, also known as Industrial Internet, is characterized by the combination of advanced internet and communication technologies, embedded systems, and intelligent machines.
Industry 4.0 provides significant opportunities for the realization of sustainable manufacturing as machines collect large amounts of data through smart sensors, communicate with each other and independently make decisions.20 These systems create and analyze big data to optimize production processes and logistics. Industry 4.0 and the Industrial Internet aim to increase productivity by reducing idle times, improving predictive and preventive maintenance of equipment and making logistics more efficient.21
In China, Industry 2.0 represents the major process framework, relying on a high number of employees rather than automation. The majority of the local or domestic companies prefer the use of labor intensive methods as opposed to the machinery due to lower capital required. In the foreign owned or the joint venture operations with foreign players, the industrial processes feature more automated methods of production. Methods such as machining, forging, heat treatment, welding and NDT by laborers are more often noted compared to robotic methods of production. Relying on labor intensive manufacturing methods, rather than smart production systems, makes it difficult to balance the technical, social, and economic elements and incorporate sustainable practices into the process.
In terms of the design processes, domestic designs generally do not focus on sustainable or end-of-life/disposal of the product compared to those designed outside of China. Locally, the international series standards and certifications of ISO 9000ii and ISO 14000iii are very important and popular for manufacturers that also target the sale of their products outside the Chinese market. Chinese designs often focus on safety and working life evaluation for the extended lifetime of the product without much emphasis on the afterlife of the product.22 The government though has set to change this by setting out stringent measures to ensure that the designs and products developed locally have a recycling plan as a measure to protect the environment as well as ensure sustainability in the Chinese market.
The Mercator Institute of China Studies carried out a qualitative assessment of the development status of industrial production in the Chinese aircraft manufacturing industry with AVIC Engineers and noted that a majority of the companies are still operating in the Industry 2.0 technology with a few implementing the Industry 3.0 and a handful implementing the Industry 4.0 technology. This presents an opportunity for Autodesk to focus their strategy around crafting products compatible to the Industry 3.0 and 4.0 technologies. A breakdown of the segmentation is presented in the table below:
3.3 Digitization of Manufacturing Processes
Worldwide, there is a greater preference to shift from the traditional methods to the digital methods of production across the value chain. In the 2018 McKinsey Digital Manufacturing Global Expert Survey, several companies worldwide indicated that digitizing production was a main priority, including their connectivity, intelligence, and flexible automation.
The transition concentrates mainly on basic digitization such as the installation of Enterprise Resource Planning (ERP) and Manufacturing Execution Systems (MES) (Industry 3.0). While China is still catching up with Industry 3.0, industrial software solutions that integrate cloud and big-data services are increasing in popularity in the Chinese market.23
Local developers have managed to create solutions at a low-costs, fitting well with the needs of both private small/medium enterprises and state-owned companies. With a good understanding of the specific needs and user-interface preferences of Chinese users, these companies deliver tailored products to Chinese SMEs that have customized methods of communication. Chinese enterprises like Yonyou, Kingdee and Digiwin are beginning to focus their strategies on new, integrated software solutions to push the development of Industry 4.0 products and processes at cater to the needs of Chinese companies.
CAD Tools
To meet country-wide codes and standards, computer-aided tools (CAD, CAE, and CAM), such as ANYSY, PV Elite, AutoCAD, and SW6, are commonly used during the design phase of products.24 Chinese university students in science and engineering fields are often required to learn these methods.
Manufacturing Methods
Although additive manufacturing adoption is relatively low due to high capital costs, this process is becoming more popular with increasing adoption of 3D printing by manufacturers throughout China.25 Since additive manufacturing is a continuously adapting industry, many firms develop hybrid models merging conventional and additive manufacturing processes to meet their specific needs.26 A comparison of the Additive and Conventional Manufacturing is presented below:
Cloud migration and budget allocation to digitization
Adoption of additive manufacturing leads to digitized processes and data migration to the cloud. Globally, about 75% of manufacturers have an ongoing smart factory or are in the process of establishing it. Additionally, nearly half of all manufacturers worldwide have invested $100 million or more towards smart manufacturing technologies.27 Utilizing cloud-based technologies brings many advantages to manufacturers, such as increase in efficiency and quality of production, as shown below.
China’s internet infrastructure is highly regulated. Foreign businesses are not allowed access to China’s cloud computing market for either the Infrastructure as a Service (IaaS) or Platform as a Service (PaaS). Thus, foreign businesses cannot access the required Internet Data Centre (IDC) license unless through a joint venture partner. The law requires localization of personal information and data collection, therefore presenting technical barriers and difficulties to both Chinese and foreign firms, while creating limited added value to security.28
Despite heavy regulation, there remains growth (between 10-25% in 2015) in the adoption of the Industry 3.0 technologies such as software, industrial robots, and sensors. Further, demand for Industry 4.0 technologies, such as big data, cloud computing, wireless sensor networks (WSN), and microelectromechanical systems (MEMS), continues to increase with growth between 20-25% in 2015.29
3.4 Made in China 2025 Initiative
The Made in China 2025 Initiative focuses on the restructuring of the country’s manufacturing industry to become more competitive in the high-tech sector.30 The initiative focuses on four key aspects including: (1) Innovation, (2) Quality, (3) Digitization of the Industry, and (4) Environmental Protection. As shown below, the government has set specific targets and deliverables within each category by 2025.
According to the China Manufacturing 2025 Report, the initiative is part of the country’s aim of entering into the global market by 2025, becoming a manufacturing leader in the market by 2035, and becoming a global leader in innovation by 2045. The Initiative focuses on the delivery of 5 key projects;
National Manufacturing Innovation Centers Project-1; to strengthen national manufacturing innovation ability.
Intelligent or Smart Manufacturing Project-2; including advanced sensors, advanced control system and industry software etc., in order to shorten the R&D time and cost.
Strengthening Industry Fundamentals Project-3; including public and service innovation platform for both large and small enterprises.
Green Manufacturing Project-4; developing clean and sustainable manufacturing technologies based on reuse, reduce and recycle principles, developing precision and ultra-precision machining technologies etc.
Innovation Project of High Level Manufacturing Equipment-5; including 10 main sectors, such as: next generation information industry, high level NC machine and industry robotics, sea and ocean engineering project, energy-efficient and new energy automobiles, equipment for aviation and aerospace industries, advance transportation equipment for railroad, energy equipment, new materials, bio-medicine and medical equipment, and agricultural equipment.
As part of the initiative, Chinese leadership sees smart manufacturing as a key tool for growth. Central to these goals in the 2025 initiative, is substituting foreign technology with Chinese brands. Many companies are considering the different ways to adapt to the initiative, for example moving out of large and expensive cities to rebuild greener factories or shifting to cleaner industries.
3.5 Challenges in the Manufacturing Sector
Worldwide, traditional manufacturing is being replaced by smart systems, with China’s industry facing three core challenges:31
- Weakness in innovation ability: Investment in research and development in China averages around 1%, compared to 3-5% in high-income countries. This is mainly attributed to the low investment in the development of products and the mass production of already-designed products.
- Limited, but rapidly growing, advanced manufacturing industrial sector: Many sectors require the importation of key components, such as aviation turbines for the C919 Airplane.
- Serious pollution and waste resource: In 2010, the GDP of China was about 7.5% of the whole world while the energy consumption was 19.6%.
4 Sustainability Approach
The Chinese government is the main driving force behind the country’s push for smart manufacturing. Prime Minister Li Keqiang indicated, “The manufacturing industry is a main pillar for the national economy, main opportunities must be used. The transition towards smart manufacturing is essential.” The administration focuses on alternative-fuel vehicles, high-tech ships, renewable energy, and robots; among others. As illustrated below, the government has set growth goals in these key sectors to enable a transition into a high-income economy.32
4.1 Drivers of Sustainability
The main drivers of sustainability within the manufacturing sector in China are cost, regulation, and innovation:
Costs of Change: Chinese enterprises are often reluctant to invest in high-tech equipment and opt for solutions with low upfront investment.33 Even though labor costs and minimum wages are increasing, employing a large workforce with low and medium skills often represents the cheaper option compared to major investment in new equipment.
Need for Free Market Competition: Many enterprises feel no pressure to undergo a lengthy and costly upgrade toward modern production capacity. These firms rely on political protection and lack incentives to strengthen market power by increasing productivity and improving production technology.
High cost of environment penalty forces: Manufacturers are taking measures to mitigate environmental pollution. State Environmental Protection Administration (SEPA) has grown to include the Ministry of Environmental Protection (MEP), established in 2008, which is responsible for establishing and implementing domestic policies associated with pollution and environmental issues. Although it is unclear how often they intervene, the MEP sets penalties for companies who do not meet their guidelines.
4.2 Sustainability Implementation
Although many Chinese companies do not have dedicated sustainability teams, many firms are still voluntarily taking actions. Different players work in various manners to achieve sustainability depending on the size and nature of a company. Both the monetary and human capital investment vary in different business and development processes. This variation is better presented in terms of the company’s ability or willingness to invest a presented below:
Incorporating sustainability into product design and development can occur in various forms. The approach to sustainability in Chinese automobile, aviation and industrial equipment sectors comprises at least three aspects: nature conservation, production-related environmental protection, and “5R” implementation: Reduce, Reuse, Remanufacture, Recycle, and Recovery.34
According to Cheng Ming, a scholar at Shanghai Jiaotong University, School of Mechanical & Power Engineering, a framework of sustainable manufacturing in Chinese industries should follow three points:
- A management system for safeguarding sustainable manufacturing should be established to provide technical and policy support to meet guidelines.
- Technical support for theory and methodology of life-cycle and end-of-life assessment of products.
- Implementation of “5R” strategy for promoting a “technology and information platform” for green design of Chinese products.
To demonstrate the capacity and possibility of green manufacturing, the Chinese government selected key companies in various sectors to provide specific support, which may be suitable candidates for further engagement by Autodesk. These key sectors range from aviation, automotive, electronics, metals and materials, energy equipment, food and medicine and ship building.
Considering the significant influence of government in the Chinese market, it is important that Autodesk formulate their sustainability strategy around these key industries. It is also noted that there is room for an increase in investment in research and development (R&D). Within the Chinese manufacturing industry, extensive R&D occurs mainly in the capital-intensive industries and enables an increase in company outputs, resulting in higher profits. As presented in the table below,35 companies in the various industries that invested in R&D, turned a higher profit. Therefore, Autodesk should orient their sustainability strategy toward the development of software or products focused in assisting the R&D process.
4.3 Efficiency in Manufacturing
The efficiency in manufacturing spans across the entire process and is best achieved as a result of concerted effort at every stage of production.36 This includes both material and labor usage efficiency. According to the Deloitte Analysis by the Deloitte University Press, improving enterprise efficiency begins by maximizing efficiency of a single asset, which transfers to a production line, then to the factory, and finally to the factory network.
5 Conclusion
Decisions that impact energy and material usage are made by designers and manufacturers who focus on safety, codes/standards, cost, and feasibility of the entire project. In the pursuit of rapid economic growth, Chinese methods of production caused severe environmental damage. Within the last few years, the government is focusing on the energy efficiency and environmental protection, which is essential to creating a self-sustaining, robust domestic manufacturing industry. These efforts aim to develop China as an economic global leader.
Footnotes
- By definition, Tier-III hospitals offer specialist services in addition to general health services.
- ISO 9000: A set of standards that address various components of quality management and assurance.
- ISO 14000: A set of standard that address environmental management.
References
- Statista (2017): China: Composition of GDP (gross domestic product) across economic sectors from 2007 to 2017. Available: https://www.statista.com/statistics/270325/distribution-of-gross-domestic-product-gdp-across-economic-sectors-in-china/
- http://www.worldstopexports.com/chinas-top-10-exports/
- IBIS world report, July 2018
- China Association of Automobile Manufacturer (2018). “The auto export enjoyed rapid growth yearly.” Available: http://www.caam.org.cn/AutomotivesStatistics/20180115/1305214913.html
- McKinsey & Company
- According to Civil Aviation Administration of China
- Agency for Growth Policy Analysis (2013); China’s Healthcare System – Overview and Quality Improvements. Available: https://www.tillvaxtanalys.se/download/18.5d9caa4d14d0347533bcf93a/1430910410539/direct_response_2013_03.pdf
- US International Trade Administration (7/25/2017): China medical-devices. Available; https://www.export.gov/article?id=China-Medical-Devices
- According to S&P Global Market Intelligence
- China’s General Administration of Customs, 2017. Available online: http://www.customs.gov.cn/customs/302249/302274/302275/1998567/index.html
- Forbes, August 2018
- Ihrcke, Joachim & Becker, Krystina & Singapore, Comp. (2018). Study 1: Machinery Study Experts: Study on the Future Opportunities and Challenges of EU-China Trade and Investment Relations.
- https://www2.deloitte.com/insights/us/en/economy/asia-pacific/china-belt-and-road-initiative.html
- Capgemini Digital Transformation Institute, smart factory survey
- J. Wübbeke, M. Meissner, M. J. Zenglein, J. Ives & C. Björn (December 2016): “MADE IN CHINA 2025: The making of a high-tech superpower and consequences for industrial countries” Mercator Institute for China Studies, No. 2.
- IFR [International Federation of Robotics] (2015). “World Robotics 2015 Industrial Robots”. Available: http://www.ifr.borg/industrial-robots/statistics/.
- According to MERICS (Mercator Institute of China Studies) the International Federation of Robotics data
- J. Wübbeke, M. Meissner, M. J. Zenglein, J. Ives & C. Björn (December 2016): “MADE IN CHINA 2025: The making of a high-tech superpower and consequences for industrial countries” Mercator Institute for China Studies, No. 2.
- 2011 Deloitte report on Where China’s Manufacturing Industry is Going
- Stock, T., Seliger, G. (2016). Opportunities of Sustainable Manufacturing in Industry 4.0, Procedia CIRP, v. 40, pp. 536-541. Available: https://www.sciencedirect.com/science/article/pii/S221282711600144X
- Waibel, et al. (2017). Investigating the effects of smart production systems on sustainability elements. Procedia Manufacturing, v. 8, pp. 731-737.
- Interview with Haoyang (Daniel) Wang, Manager Technology & Business Development, ASME Beijing.
- Made in China 2025 Report
- Interview with Haoyang (Daniel) Wang, Manager Technology & Business Development, ASME Beijing.
- Interview with Yang Yi Peng, Portfolio & Credit Risk Manager, China Youth Travel Services Financial Leasing Co. Ltd
- VDI and ASME, Apr 2017
- Capgemini Digital Transformation Institute, smart factory survey, Feb-Mar 2017
- European Chamber on China Manufacturing (Feb. 2017).
- Made in China 2025 Report
- IFR [International Federation of Robotics] (2015). “World Robotics 2015 Industrial Robots”. Available: http://www.ifr.borg/industrial-robots/statistics/.
- China Academy of Engineering
- Expert Commission for the Construction of a Manufacturing Superpower
- J. Wübbeke, M. Meissner, M. J. Zenglein, J. Ives & C. Björn (December 2016): “MADE IN CHINA 2025: The making of a high-tech superpower and consequences for industrial countries” Mercator Institute for China Studies, No. 2.
- VDI & ASME (2017): The Digital Engineer and The Changing Workplace. Available: http://www.vdi.eu/fileadmin/vdi_de/redakteur/bg-bilder/ASME/z02_ECE_Student_Study_WEB.pdf
- Report from Mercator Institute of China Studies
- Interview with Wei Sheng, Product and Manufacturing Manager, CHTC Motor
No Comments.