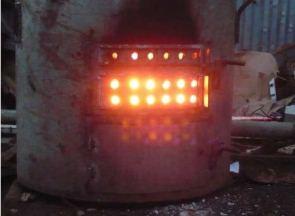
Agriculture
January 10, 2024
T4T Mak IV Incinerator
Read SolutionImplemented by
Technology for Tomorrow (T4T) Africa
Updated on January 10, 2024
·Created on August 1, 2019
The De Montfort medical waste incinerator is a low-cost and effective medical waste incinerator which can be built in almost any developing country.
The De Montfort medical waste incinerator reduces all medical waste added to ash and flue gases, including dressings, plastics, and organic matter. Needles may not all be reduced though they will be sterilized. The De Montfort incinerators were designed by Professor D.J. Picken, over a period of about 8 years from 1996 to provide a low-cost and effective incinerators which could be built in almost any developing country.
Target SDGs
SDG 6: Clean Water and Sanitation
Market Suggested Retail Price
$1,500.00
Target Users (Target Impact Group)
Small and Medium-sized Enterprises, Public Sector Agencies
Distributors / Implementing Organizations
WHO, MSF, the British Council, UNICEF, the Salvation Army and Technology Without Borders
Competitive Landscape
Direct competitors include T4T Mak IV Incinerator.
Regions
Worldwide
Manufacturing/Building Method
Manufactured locally, with schematics and instructions available online
Intellectural Property Type
Open-source
User Provision Model
The designer, Professor D.J. Picken, provides schematics online so the incinerators can be manufactured locally using the provided schematics. NGOs have used these designs.
Distributions to Date Status
Over 1,000 distributions worldwide.
Capacity (kg)
The Mark 8a model burns 12 kg/hour, and the Mark 9 burns 50 kg/hour.
Type of energy
Fire-power
Energy Requirement (kWh)
N/A
Run-time (min)
One box of syringes every 10 minutes.
Design Specifications
The De Montfort Mark 8a has a capacity of 12 kg/h and takes 3-4 days to build. There is a concrete foundation of L x W x H = 2 m x 2 m x 0.15 m and refractory bricks of L x W x H = approx. 230 x 110 x 65 mm (the mortar is refractory cement (high alumina)). The body will have 13 layers. Other components include the top frame, loading door, ash door, chimney, shelter, and outer wall.
The De Montfort Mark 9 has a capacity of 50 kg/h and takes 5-6 days to build. For the foundation, a concrete platform of at least 3 m x 2 m x 150 mm thick should be prepared on the chosen site, ideally with a roof about 3 m high to protect the incinerator and the operator from weather. The body will have 14 layers. Other components include the top frame, loading door, ash door, chimney, shelter, and outer wall.
List of materials and their dimensions for the Mark 8a and Mark 9 can be found on the instructions for the model.
Technical Support
Technical support is provided in an operation manual and maintenance instructions, otherwise users are expected to maintain the incinerator on their own.
Replacement Components
The chimney, chimney support plate, sand seals, ash door, and bricks all need to be maintained and replaced as needed.
Lifecycle
3-5 years
Manufacturer Specified Performance Parameters
The incinerator was designed to meet the criteria of a temperature of above 800oC with a residence time of over 1 second.
Vetted Performance Status
The original (Mark 1) incinerator had been tested by CSIR, in South Africa, in December 1999. Representative samples of waste from a typical primary health care centre were prepared by the South African Department of Health at the CSIR testing facilities. The principal findings were: “The medical waste tested in the trial was rendered non-infectious, the syringes were destroyed and the needles were rendered unsuitable for use. The emission of particulates, metals and chlorides comply with South African regulations for primary health care clinical waste used in the South African trials on small scale incinerators and the fuel to waste feed conditions for the tests. The combustion efficiency does not comply and the organic emissions are higher by a factor of at least 20 times.” The author noted that the test had been carried out at temperatures below 600°C, and that an undue quantity of wood was burned during the tests, which contributed to the high organic emissions. The next test was of a Mark 2 incinerator at the De Montfort University and was reported by DJ Picken in January 2001. The principal findings were: 1. “The combustion chamber temperature was above 800°C for most of the test; 2. For most of the running time there was no visible smoke emission. Only rarely did the smoke level exceed that which is considered acceptable in a diesel engined road vehicle; 3. Such smoke as was collected proved to contain only carbon. No metallic elements were present; 4. The flue gas was found to contain virtually no dioxins or furans. 5. Oxygen level in the flue gas varied between 4% and 16% 6. Carbon monoxide level was mostly in the region of 100 ppm, with levels above 400 ppm occurring only rarely.” A third test was carried out on the Mark 3 incinerator in the presence of observers from Médecins Sans Frontières in December 2000. Again the results were reported by DJ Picken. This test was carried out to test the efficacy of the incinerator to burn wet textiles as well as general clinical and household waste. The principal results were: “In all cases, at least one of the temperature zones through which the flue gas had to pass exceeded 800°C. CO could not be measured precisely at this low value. O2 levels fluctuated depending on how recently the load door had been opened, and the type of load. Rate of burning was very high, in the region of 50kg/h, again depending on load material. This meant that loading had to be very frequent, in the region of every 5 minutes.” For the fourth test, a Mark 8a incinerator was constructed at a site in Leicestershire and 8000 hypodermic syringes were sent to the site by WHO. Casella CRE Emissions of Cheltenham were engaged to sample and analyze the exhaust gases, and the incinerator was operated by the designer and a technician. Two 2-hour tests were carried out, one at maximum loading rate, and one at a loading rate designed to limit smoke production. Loading rates, temperatures and smoke levels were recorded as well as the gas samples. In both cases none of the 12 dioxin-like PCBs targeted were detected in the samples collected, although detection limits were substantially higher than usual. In both tests, the temperature of the gas path reached 800°C for nearly the whole test. Smoke levels were unacceptably high for test one where loading rate was at a maximum, but lower for test 2. A WHO assessment of De Montfort Incinerators in Tanzania found, "Out of 26 incinerators found during the assessment only 2 (7.6%) were not De Montfort models. Keeping De Montfort incinerators functioning appeared to be the main challenge. The study found that out of the 24 incinerators assessed, 7 (29%) were had not been operating for a period varying of 2 months to 3 years, mainly due to structural defects, which seemed caused by the non-adherence of contractors to use recommended construction materials, and particular specifications and designs for De Montfort incinerator to operate properly and at the right temperature. The study revealed that all of the 7 non-functioning incinerators had been constructed of burnt bricks obtained locally rather than the recommended firebricks." Toxins released can be viewed in the report.
Safety
Complementary Technical Systems
None
Academic Research and References
Amfo-Otu, R., et al., 2015, Comparative study of heavy metals in bottom ash from incinerators and open pit from healthcare facilities in Ghana. Octa Journal of Environmental Research, 3, pp. 50-56.
Adama, M., Esena, R., Fosu-Mensah, B., & Yirenya-Tawiah, D., 2016, Heavy metal contamination of soils around a hospital waste incinerator bottom ash dumps site. Journal of Environmental and Public Health. Vol 2016.
Picken, D. J., & Bennett, M. C., 2000, The design of a small, cheap and versatile medical waste incinerator for use in developing countries.
Picken, D. J., & Bennett, M. C., 2002, The design of very low cost incinerators for emergency situations in developing countries.
Akufo-Kumi, K., et al., 2014, Design, construction and test operation of a thermal incinerator for medical wastes at Abokobi Health Centre, Ghana. Journal of Applied Science & Technology, Vol. 19.
Manyele, S. V., Anicetus, H., 2006, Management of medical waste in Tanzania hospitals. Tanzania Journal of Health Research. Vol 8.
Di Bella, V., Ali, M., Vaccari, M., 2012, Constraints to healthcare waste treatment in low-income countries–a case study from Somaliland. Waste Management & Research, 30, pp. 572-575.
Batterman, S. 2004, Findings on an Assessment of Small-scale Incinerators for Health-care Waste. World Health Organization.
Compliance with regulations
Depends on location.
Evaluation methods
The manufacturer evaluated the incinerator and states when properly operated it will achieve 800°C for at least one second and provides these disclaimers.
Other Information
The instructions for this model (The De Montfort Mark 8a) can be found here.
The instructions for this model (The De Montfort Mark 9) can be found here.
Technical support is provided in an operation manual and maintenance instructions.
Other chemical detection can be viewed in the report.
Operation and maintenance instructions are found here.
Links to laboratory testing for air pollutant emissions is found here.
Emissions Tests on De Montfort Medical Waste Incinerators can be found here.
Agriculture
January 10, 2024
Implemented by
Technology for Tomorrow (T4T) Africa
Agriculture
January 10, 2024
Implemented by
HLL Lifecare Limited
Agriculture
January 22, 2024
Implemented by
Sanivation
Agriculture
January 19, 2024
Implemented by
Clean Team Ghana
Agriculture
August 17, 2024
Implemented by
Sanergy
Agriculture
January 17, 2024
Implemented by
Sanima
Agriculture
November 22, 2024
Implemented by
Appropriate Energy Saving Technologies Limited (AEST)
Agriculture
February 3, 2024
Implemented by
Greenpact
Agriculture
January 21, 2024
Implemented by
Cambridge Industries Ltd.
Agriculture
December 27, 2023
Implemented by
Aquabox, UK
Have thoughts on how we can improve?
Give Us Feedback