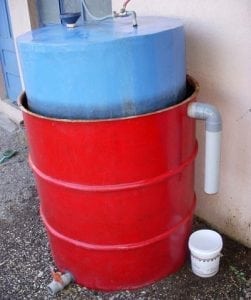
Agriculture
December 18, 2024
TINYTECH Portable Biogas Plant
Read SolutionImplemented by
Tinytech Plants
Updated on January 21, 2024
·Created on June 5, 2014
The MBSA Biogas Plant is a system that uses waste created from Jatropha oil processing to produce biogas.
The MBSA Biogas Plant is a biodigestor developed by MBSA to produce biogas from Jatropha nut oil extraction sites and surrounding rural communities. A Jatropha nut seedcake is a by-product of the nut oil extraction process, and is mixed with human or animal waste and water in the Biogas Plant to produce biogas for use in cooking or to fuel a generator.
Target SDGs
SDG 7: Affordable and Clean Energy
SDG 8: Decent Work and Economic Growth
Market Suggested Retail Price
$200.00
Target Users (Target Impact Group)
Household
Distributors / Implementing Organizations
This product is implemented by MBSA in partnership with FACT Foundation.
Competitive Landscape
Direct competitors include Sistema Biobolsa, Flexi Biogas BG5, and SimGas GesiShamba.
Countries
Burkina Faso, Mali
Manufacturing/Building Method
This product is manufactured by MBSA for use at one of their Oil Extraction Sites (OSE), and at least five of these sites have been manufactured in Mali and Burkina Faso. Manufacturing method is currently on a per demand basis from fiber-reinforced PVC, and the connecting pipes are also made from PVC.
Intellectural Property Type
Trademark
User Provision Model
MBSA supplies 3 regions of Mali and 2 regions in Burkina Faso with industrial scale machinery to service up to 12,000 farmers per region. The MSBA Biogas Plants can be used in conjunction with these sites.
Distributions to Date Status
As of 2012, five Oil Extraction Sites (OES) and five Multifunctional Platforms (MFP) have been distributed.
Output energy product
Unknown
Average daily biogas production (m3/day)
2.71
Description of waste source(s)
Animal dung mixed with Jatropha press cake
Waste input requirements (kg per hour or day)
5 kg solid mass per day
Description of other input requirements
Water
Other input requirements (amount per hour)
8 L per day
System dimensions (m)
10 m
Design Specifications
The MBSA Biogas plant is a plug flow type digester made of a fibre re-enforced PVC bag of 10 m3 for anaerobic digestion. Inlet and outet connections are made through 110 mm PVC pipes, and the air input is achieved through an aquarium pump that injects air into the bag through a small plastic hose. A plastic valve is also in place to control the air flow in the system, and a 20W photovoltaic system supplies electricity for the pump. Additional components like a condensation trap, a flow meter, a pressure release system with pressure meter, and 3 valves (gas network control), are required.
The system has a length of 7.0 m and a width of 2.6 m.
Technical Support
Training needs and support provided by MBSA staff.
Replacement Components
Replacement components can be sourced through MBSA foundation and manufacturing plants. MBSA understands and focuses on the need for simple replacements using in-country supplies.
Lifecycle
Unknown
Manufacturer Specified Performance Parameters
The manufacturer specified targets are to add value to the farming of Jatropha, increasing crop yield rates by 20% in five years, and to add an additional income of ~1 USD per day to farmers.
As part of this process, the SOXHLET is designed to press 3,000 kg of Jatropha seeds per hour , yielding 0.29 kg of oil per 1 kg of seeds.
Vetted Performance Status
Testing of biogas input, performance and effectiveness of liquid/solid separation for use as a fertilizer was conducted in 2011 by Kevin Chapon from AVANS Hogeschool working with MBSA and FACT. These are some of the findings: • The hydraulic retention time of the system is set at 50 days, so the daily input of feedstock is 1/50 of the digester volume. • Wet mixture represents 6 m3, so the daily input should be 120 liters. • The supply of the digester started with 35 kg of cattle dung associated to 55 liters of water during the first month. The amount of manure was decreased by 5 kg every two weeks while adding Jatropha press cake to the mixture. After two and a half months, the digester was supplied by 15 kg of manure and 8 kg of Jatropha press cake. • The average daily biogas production is 2.71 m3/day.
Safety
One of the by-products of the digester is hydrogen sulphide, a colourless, very poisonous, flammable gas with the characteristic foul odour of rotten eggs at a concentration up to 100 ppm.
Complementary Technical Systems
Complimentary technical systems include a 20 W solar powered air pump.
Academic Research and References
The most useful and relevant academic paper is by Kevin Chapon from Dutch AVANS School who did his thesis work with MBSA’s biogas system on separation of effluents for fertilizer use:
Chapon, K., 2011, Utilisation of the effluent of a plug flow digester. Bachelor Environmental Technology & Management Final year project with FACT Foundation. Environmental Technology & Management, Avans University of Applied Science, Breda, Netherlands.
As MBSA’s biogas systems are still under development there are no peer reviewed journals on their biogas system. However there are papers on general biofuel development in Mali and use of Jatropha nuts that involve MBSA:
Achten, W., Maes, W., Aerts, R., Verchot, L., Trabucco, A., Mathijs, E., Singh, V., Muys, B., 2010, Jatropha: From global hype to local opportunity. Journal of Arid Environments. Volume 74. Issue 1. pp 164-165.
Basinger, M., Chen, J., Jeffrey-Coker, F., Rodriguez-Sanchez, F., Singer, T., Modi, V., 2012, Jatropha adoption: a statistical observational study of factors influencing Malian farmers’ decision to grow Jatropha. Agroforestry Systems. Vol 84. Issue 1. pp 59–72.
Two useful articles on flexi biogas plants:
Sehgal, K., Wanjihia D., Kembe M., 2012, Flexi Biogas systems: inexpensive, renewable energy for developing countries. International Fund for Agricultural Development.
Vijay, V., 2014, Technical and field performance evaluation of flexi biogas plants. International Fund for Agricultural Development.
Voila , Malime. 2011. Companies. ETM Student in Mali (blog). March 17, 2011.
Slager , A.A. 2012. Design of a Flaring System for Small and Medium Scale Biogas Installations in Rural Mali. Bioenergyforumfact.org. Wagningen, Netherlands: FACT Foundation, Wageningen University.
Almeida, J., Moonen, P., Soto, I., Achten, W., Muys, B., 2014, Effect of farming system and yield in the life cycle assessment of Jatropha-based bioenergy in Mali. Energy for Sustainable Development. Vol 23. Issue 1. pp 258-265.
Compliance with regulations
None specified by MBSA. FACT Foundation's mandate is to develop biofuels in accordance with European quality standards.
Evaluation methods
Methods referenced in testing by Kevin Chapon (MBSA/FACT) include comparing best drying technique of the affluent via passive solar radiation vs straw filtration, as well as comparison of traditional fertilizer performance with that of biogas by-products as fertilizer.
Other Information
Performance can be improved through better anaerobic digestion process, general system efficiencies improvements, incorporation of techniques and technologies to allow for various biofuel inputs, increasing biogas conversion rate, reducing water input and/or recovering some of the water through system recycling and re-use. Improving ways to recover and utilize biogas by-products (effluent) as a fertilizer can also lower operation costs, reduce payback period, and increase a farmer's income. As some power is also required for operation, connecting to a complementary and readily available source of power like solar PV can be very useful.
Agriculture
December 18, 2024
Implemented by
Tinytech Plants
Agriculture
January 28, 2024
Implemented by
Appropriate Rural Technology Institute (ARTI)
Agriculture
December 17, 2024
Implemented by
Biogas International Limited
Agriculture
December 16, 2023
Implemented by
Green to Energy (G2E)
Agriculture
December 16, 2023
Implemented by
Husk Power Systems (HPS)
Agriculture
December 16, 2023
Implemented by
NETPRO Renewable Energy (India) Pvt Ltd
Agriculture
May 27, 2024
Implemented by
Development Technology Workshop
Agriculture
May 27, 2024
Implemented by
Montals Engineering
Agriculture
December 19, 2024
Implemented by
Green Heat
Agriculture
January 18, 2024
Implemented by
Agua Clara LLC
Have thoughts on how we can improve?
Give Us Feedback